仕事
夏を過ぎれば大きい工程が終わり、少しは時間に余裕が・・・
と思っていたら、次から次へと新たなオーダーが積まれていく。
勿論、仕事量の増加=収入増、だから喜ばしいことではあるのだけど
さすがに疲労気味。
ようやく仕事の流れも理解出来てきて、そこそこの大物も任されるようになってきた。
さすがにこの道何十年という人には敵う筈も無いけど、求められるのは速さよりも正確さ。
とか言いながらも、やっぱりモノを作るって言うのは奥が深い。
図面を見て、その通りに正直に作ると失敗する。
ココとココをこうやって繋ぐんだから、コレくらいの脚長の溶接でいくと恐らく2mmは縮むはず・・・
だから2mm大きく仮組みしておこう、とか
コッチから溶接を始めるとコッチに反るから、あらかじめコッチにテンションかけておこう・・とか。
図面、工程には無い治具を廃材を利用して作ったり。
自分は溶接工ではないので、溶接は職人さんに任せる。
彼らは数十年、溶接技術だけで生きて家族を養った人たち。
腕前は本当にスゴイ。
無茶な姿勢でも、片手だろうが、見えない場所だろうが文句も言わず淡々とこなしていく。
その人たちの仕事を生かすも殺すも自分のセットアップ次第って言うのは結構なプレッシャー。
どんなに完璧な溶接でも、寸法的にアウトならそれはただの重さ数十トンの鉄ゴミになってしまう。
ちなみに溶接って、重要構造物の場合はただくっつけて終わりではない。
まあ、ただくっつけるといっても重要部分はFP溶接(フルペネレーション溶接)といって、母材同士をガウジングで掘り込んで表面だけでなく内部から完全一体化させる。
つまり、溶接ビードを削り落としたとしても、材料同士は完全にくっついた状態。
つまり、溶接ビードを削り落としたとしても、材料同士は完全にくっついた状態。
そうしてその後
表面傷をチェックする磁粉探傷試験
内部の溶接欠陥をチェックする超音波試験、レントゲン試験をクリアして初めて溶接が終わる。
試験だから自社でなく検査会社に一任する、検査会社には一切融通は効かない、容赦なく厳しい試験が行なわれる。
通常、屋内の工場で使用される半自動溶接(炭酸ガス溶接)は最も手軽で早く溶接できるけど、
最も溶接欠陥を生じやすいという反面もある。
溶接中に送風機の風が当たったり、母材に塗料、サビがあったり、溶接電流/電圧を誤るともうダメ。
だから溶接歴2年、3年じゃ重要部分は一切手を出させてもらえない。
そんなこんなで先月、某火力発電所が某国に設置するアンローダーを製作、完了した。
アンローダーってクレーンの一種で、港に停まった石炭を積んだタンカーからダイレクトにベルトコンベアで石炭を陸揚げするクレーン。
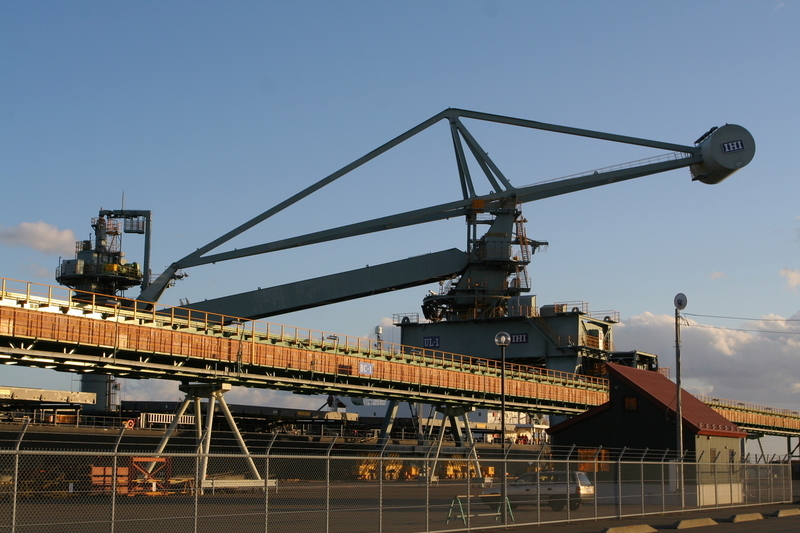
これと似たようなの(画像はずっと昔に作った物らしい)。
これを今、構内で仮組みし試験作動させている。
動作確認できたら、また分解。
某国まで船で引っ張って持っていくらしい。
総重量1200トン。
で、こんなもの船で引っ張るんだからそれ用の固定台が要る。
今度はコレを船で引く為の固定台、治具をまた数カ月がかりで製作・・・
トータル何年がかり?
その傍らでは公共事業、橋梁のブロック製作も同時進行。
東京湾に架けられる橋も、ここ広島で作ってます。
で、TMRのセッティングさえ取り掛かれない疲れ果てた私。